How to Build Custom Shop Floor Data Collection That Matches How You Actually Work
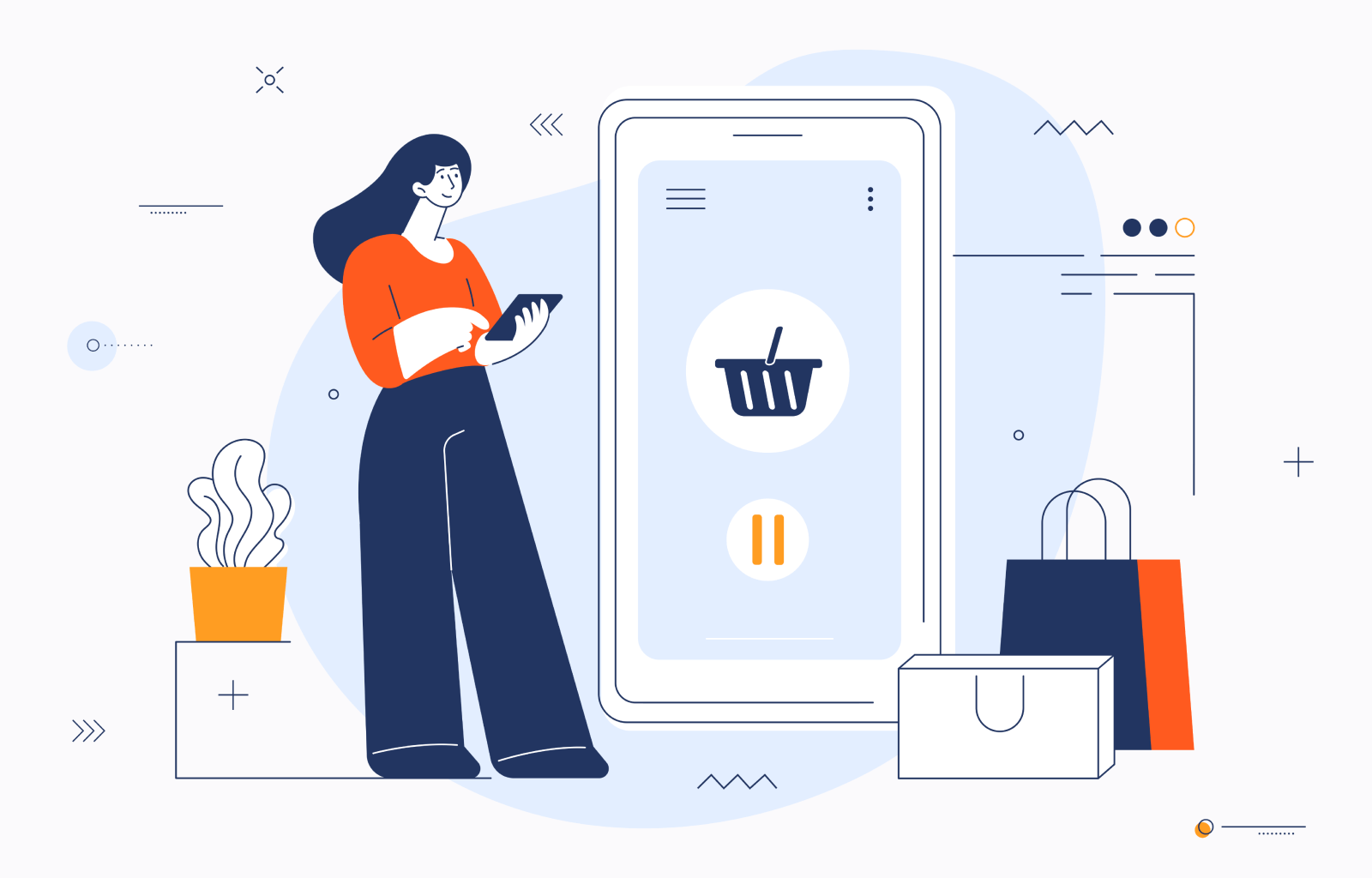
Most factories understand the importance of shop floor data collection. However, when it comes to actually doing it in a way that is consistent, reliable, and easy-to-use, things often fall apart. Many companies haven’t updated their manufacturing data collection processes in a very long time and a large percentage of them are hesitant to do so. That means their systems often aren’t as thorough, detailed, or effective as they could be.
Unfortunately, when manufacturing data collection fails (or when the processes fall by the wayside), it can mean problems for your business.
Why Most Shop Floor Data Collection Fails
Many companies still rely on handwritten logs or spreadsheets for shop floor data collection. While this is certainly better than not keeping track of downtime, output, or important stats and issues at all, it’s also not really the best option either. Manual systems are more likely to contain unnoticed errors, they’re often not properly integrated with other company systems, and they tend to require a lot of manual effort.
As a result, the numbers are frequently out of date or inconsistent when they’re even there at all. This results in staff and management losing trust in the data, which makes it even less likely that people will keep tracking.
Instead of dealing with these struggles and their consequences, why not build a shop floor data system that actually works for your company?
What Custom Shop Floor Data Systems Really Means
When some business owners or management teams hear the phrase “custom shop floor data systems” they immediately think “expensive”, “complex”, or “too overwhelming.” However, the reality is far different. The right system doesn’t make your work slower, more complicated, or more confusing. Instead, it makes you more efficient.
That’s because the right system is one that is built to follow your action steps on the floor and how you work. It isn’t designed for someone else; it’s made for your business. It doesn’t force your team to adapt to new processes or follow a rigid system that doesn’t work for you. Instead, it focuses on what is already working for your company and it functions alongside your team, giving you the processes and customizable data collection options you need.
This ease of use means staff will be more likely to adopt it, it will smoothly integrate into what you’re already doing, and you won’t need to struggle with it or fight against it.
With the right system, you’ll be able to track downtime, operator time per station, material consumption, time spent per task, workstation usage, and other factors that are important to your business. When you combine this with an interface that’s clean and easy to use, you end up with a system that improves manufacturing workflow automation and provides serious benefits for your company.
What a Good System Actually Looks Like
Even for companies that understand the importance of factory floor software and automated manufacturing data collection, it’s often hard to visualize what a good system actually looks like.
While each company is definitely different (and choosing a custom system designed with your needs in mind is incredibly important), there are a several aspects that you will want to consider when it comes to building production monitoring tools and data tracking.
Touch-friendly
- A lot of companies are still using industrial data systems that work on laptops or desktop computers. The reality today, however, is that a tool that requires a large computer is often inconvenient to use, even if that tool can run on a small laptop. This is especially true in environments that are dusty or greasy.
- Having a system that is touch friendly and can run on a tablet is much more convenient and user friendly. Tablets can go basically anywhere without difficulty.
Works offline, syncs later
- No matter what kind of internet connection your business has, you can still experience technical issues. While software that backs up and syncs to the cloud is important, you’ll want a tool that can work offline and sync later. Otherwise, you might end up unable to use your system in the result of an internet outage or weak connection.
Tracks time of each user entry
- Tracking information entered into the system is obviously important, but knowing when this data was entered is also crucial. This lets you confirm that your information is up to date, which is a vital part of manufacturing data collection.
Role-based views
- Not everyone who uses the shop floor data collection system needs to see the same information or have the same permissions. If the software behaves exactly the same for everyone, it can quickly become too complex for most users and even lead to errors or other data collection issues. By allowing role-based views, you can make sure that people only see what they need to see.
Smart defaults
- One of the goals of a custom shop floor data collection system is to have a tool that is easy to use while still giving you the information you need. An effective way to accomplish this is through smart defaults or pre-filled fields. When users don’t have to enter all the information manually, they’ll be a lot more likely to use the system.
No duplicate entry
- You’ll want to make sure that your system can recognize duplicate data and filter it out, as this will help keep your numbers accurate. This is a significant factor when it comes to manual data tracking vs digital, so it’s important to include in your software build.
Syncs to ERP or MES on your schedule
- The best industrial data systems sync with manufacturing execution systems (MES) and enterprise resource planning (ERP) software. However, you want to make sure it does this on your schedule. Otherwise, your software or your network can get bogged down by constant syncing when all you want to do is work.
Simple UI built for speed and clarity
- Again, if a system isn’t quick and easy to use, people simply won’t use it (or they’ll get frustrated when they try). That’s why you should aim for speed, clarity, and a user-friendly UI (user experience) when you build a shop floor data system.
What You Get When It Works
The right shop floor data collection system can provide serious benefits for your business. As they say, information is power and, in a manufacturing, warehousing, or factory environment, the right information helps you be more productive.
You’ll be able to make better decisions, maintain compliance, eliminate bottlenecks, and reduce errors.
Specifically, using a custom shop floor data collection helps you:
- Ensure that everyone is using the same data
- Make fewer mistakes
- Complete reports more quickly
- Avoid lengthy manual clean-up
Through accurate real-time data capture, your team will be able to make decisions backed by accurate and timely numbers, not estimates or incomplete information. Paper-based recording or spreadsheet data collection can often be inaccurate or chaotic. It may only give you some information, and compiling everything you need into one place is difficult if you’re pulling data from all over the place in different formats.
By using an effective digital shop floor data collection system built specifically for your business, you’ll always have all the information you need to make decisions, work more efficiently, and streamline your business processes.
Want to learn more about the benefits and how you can build the right tools for your needs? Ready to start creating the perfect shop floor data collection system for your business? Contact us today to get started.
Contact us
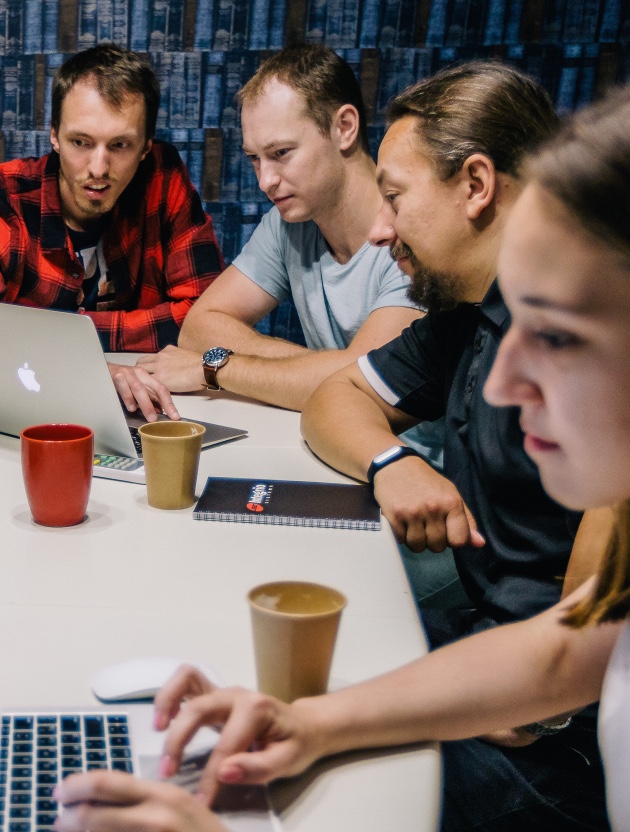