Manufacturing Agility: How to Integrate Custom Tools Without Disrupting Operations
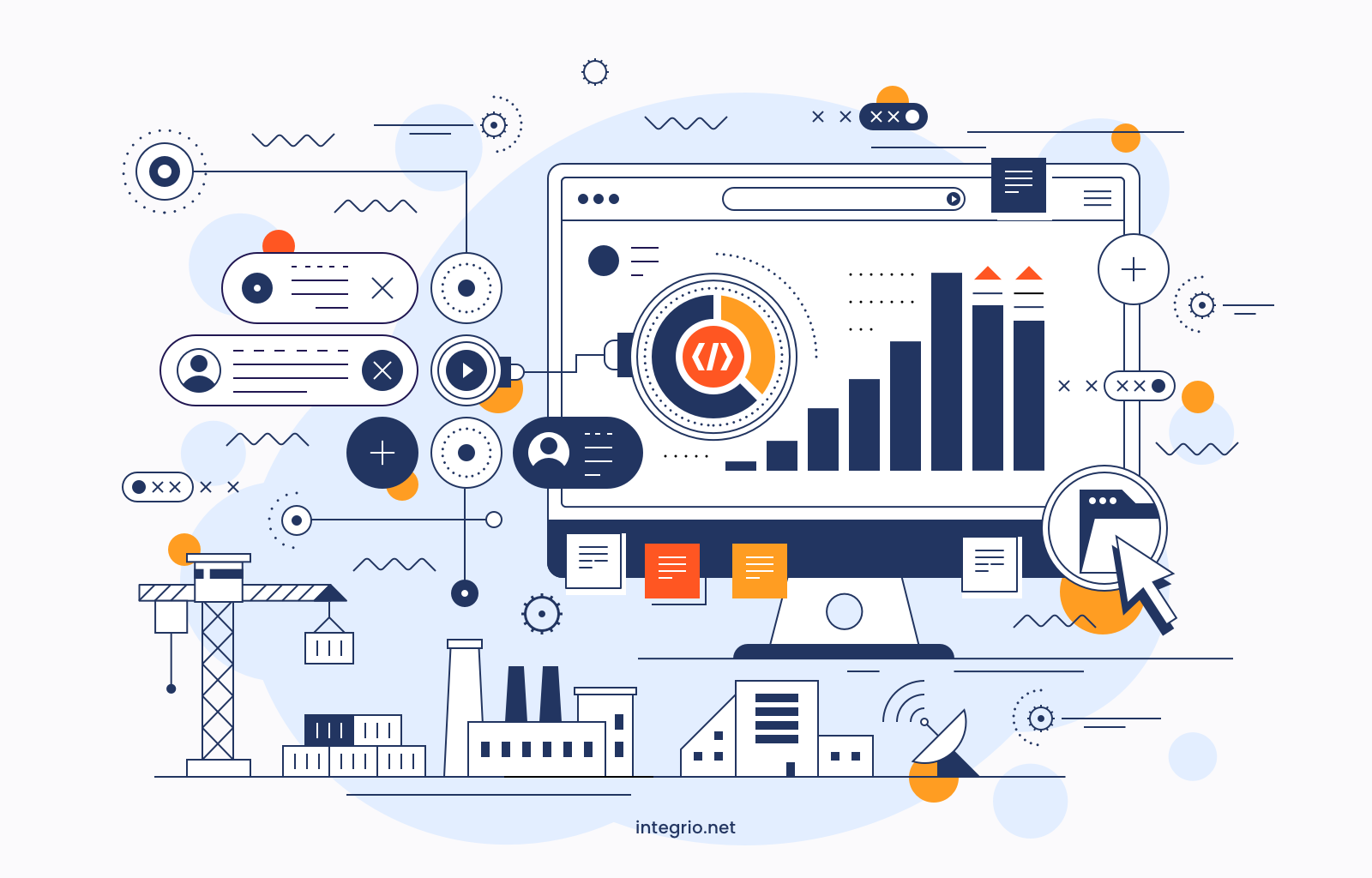
When you hear “manufacturing agility,” what comes to mind first? Probably the ability to adapt quickly when things change — and you’d be right. Whether it’s a sudden demand spike, a supplier issue, a workforce shortage, or last-minute product tweaks, agility means you can adjust without disrupting your operations.
And the best part? Becoming agile doesn’t mean throwing away your existing systems and going Industry 4.0 overnight. Often, it’s about targeted improvements — using the right tools at the right time. Many manufacturers are doing just that. 41% focus on production performance, 34% prioritize cybersecurity, and the list goes on.
That tells us one clear thing: Manufacturers want to evolve. But they also want tools that work without causing major disruptions. So how do you stay flexible and upgrade without slowing everything down? Let’s figure this out.
Why Traditional Manufacturing Systems Limit Agility
If you’ve ever tried to push a change through a traditional manufacturing setup, you know how difficult it can be. Rigid ERPs, spreadsheet-driven workflows, and siloed legacy software just don’t contribute to agility manufacturing by any means. Here’s how they hold you back:
Change requests that take weeks. Need to update a process or adjust a production line? With older systems, even small changes can trigger a domino effect — forms, approvals, custom coding, or worse, waiting on an external vendor.
Delays in responding to production issues. When a machine breaks down or a process goes wrong, fast action is critical. But if your systems are disconnected or if your team still uses paper logs, diagnosing and fixing the problem takes way too long.
Poor data visibility slows down decision-making. If your data is stored across different systems and departments, you can't make smart, timely decisions. By the time you’ve gathered a complete picture, the moment for action has already passed. It’s no surprise that 27% of manufacturers cite a lack of visibility and flexibility as a top risk if they don’t evolve their systems.
Custom Tools for Manufacturers That Can Help Support Agility
As we said, you don’t need a complete system overhaul to become more agile. The right tools are all that’s necessary. Let’s look at several agility engineering & manufacturing solutions that are making a big impact on the shop floor:
Lightweight Dashboards for Production and Shift Monitoring
Sometimes, better visibility is all it takes to increase factory automation agility. Using lightweight, real-time dashboards lets you track key KPIs — like downtime, cycle time, and throughput — by shift, line, or machine. With such solutions, you no longer have to rely on yesterday’s reports. Instead, you spot issues as they happen and respond quickly.
Flexible Scheduling Tools That Sync with ERP
You probably know how difficult it can be to adjust rigid ERP modules. But with custom scheduling tools, you can drag and drop or dynamically reorder jobs based on real-time events — like machine breakdowns or rush orders — without reconfiguring the entire ERP. Plus, these tools still sync with ERP data, so everything stays up to date.
Line-Level Inventory Usage Tracking Tools
Standard ERP systems often give you a big-picture view of your inventory. But what about material usage at the machine level? Custom manufacturing tools monitor real-time consumption at specific workstations or production lines, helping you avoid shortages, improve restocking, and reduce excess buffer stock.
Custom APIs to Link Siloed Systems
Disconnected systems are one of the biggest roadblocks to implementing agile manufacturing strategies. Custom APIs help solve that by connecting ERPs, MES, WMS platforms, and even those spreadsheets your team still relies on. These integrations enable smoother workflows, eliminate duplicate data entry, and give you plant-wide visibility without needing full software replacement.
Mobile Interfaces for Floor Teams and Supervisors
Agility is often about mobility. With mobile tools, supervisors, operators, and maintenance leads can access production data, alerts, or task checklists right from the floor. That means faster responses, fewer delays, and less running back and forth to a desktop terminal.
When Manufacturers Should Consider Custom Tool Development and Integration
You’ve seen that custom tools are perfect. But how do you know when to invest in custom manufacturing software? If you’re experiencing any of the following pain points, building and integrating tailored tools might be necessary:
Processes are too slow to adapt to customer or supplier changes. If your team finds it difficult to shift schedules, reallocate resources, or update production plans on customer or supplier requests, your systems are likely too rigid. Agility engineering and manufacturing starts with responsiveness. And if small changes outside your walls cause major internal disruptions, custom tools can help.
Teams are building workarounds in spreadsheets. If your floor managers are building complex Excel workarounds to get things done, that’s concerning. This usually means your current systems aren’t giving them the needed features. While spreadsheets are useful, they’re also error-prone, hard to scale, and impossible to keep in sync with real-time production. A custom tool can automate that.
There’s no real-time visibility into production, inventory, or quality. You're already behind if you have to review end-of-day reports or handle manual checks to understand what’s happening on the floor. Real-time visibility into machine performance, material levels, or quality issues lets you make faster decisions. If your current setup can’t deliver that, a custom dashboard or non-disruptive tool integration might be necessary.
Data is duplicated manually across tools. Are you still copying and pasting data between systems? That’s not just tedious. It’s also risky. Manual duplication leads to errors, delays, and version-control issues. If your team is spending more time inputting data than using it, custom integrations or APIs can make the entire process simpler and keep all your systems synchronized.
Conclusion
Agility doesn’t have to mean a massive transformation. More often, it’s about incremental, lean manufacturing upgrades that target your biggest bottlenecks. From real-time visibility to faster changes, implementing the right custom tools can make a huge difference without disrupting your day-to-day operations.
However, building and rolling out these custom solutions requires more than just technical expertise. It also calls for careful change management in manufacturing. That’s the only way you can increase manufacturing agility.
So if your current systems are slowing you down, or if your team is patching gaps with workarounds, you might need a more tailored solution. In that case, count on Integrio Systems. As a custom manufacturing software development company with over 20 years of experience, we’ll bring agility to your operations without turning everything upside down.
Contact us
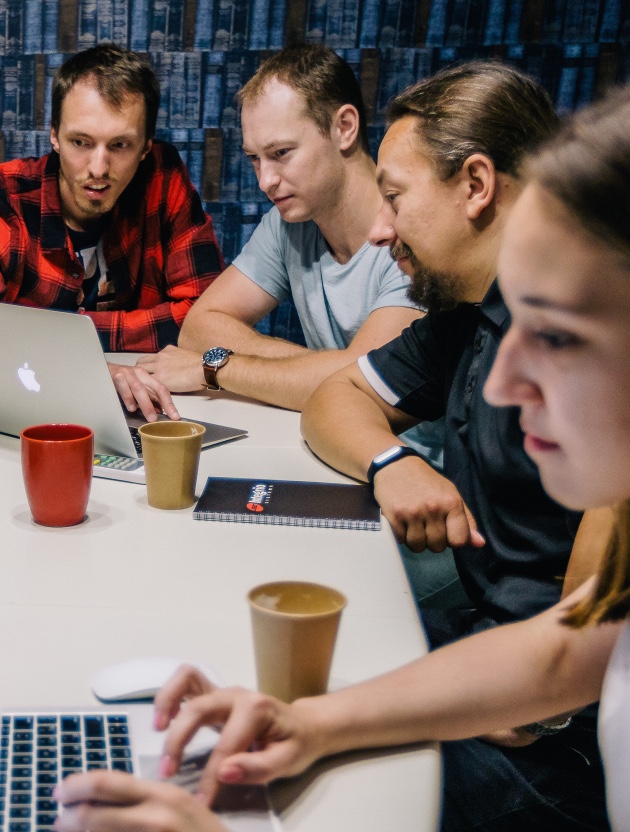