From Spreadsheets to Real-Time Dashboards: How to Build and Integrate the Right Manufacturing Analytics Solutions
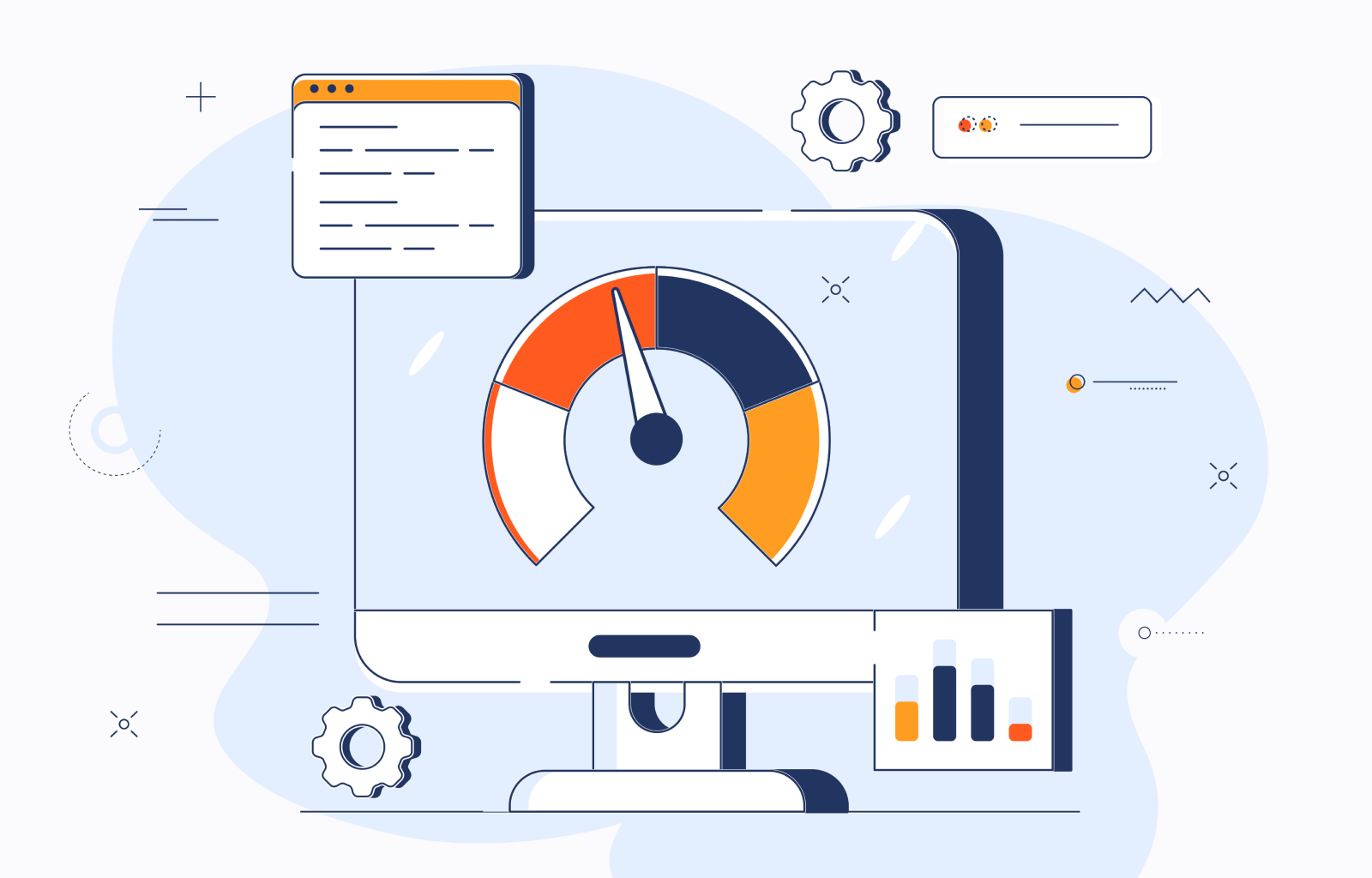
You’re collecting more production data than ever — ERPs, sensors, machines — all of it. And if you’re still making decisions based on manual reports, lagging spreadsheets, or disconnected systems, you’re not alone. In fact, only 16% of manufacturers have real-time visibility of their production lines.
Here’s the thing: Truly effective manufacturing analytics isn’t just about throwing dashboards on top of your data. It’s about building the right data foundation, architecture, and integration strategy so you can actually act on insights. In this article, we’ll explain how to move from static reports to manufacturing analytics tools that make a tangible difference across your operations.
Understanding Your Current Data Landscape
Before you can build real-time manufacturing analytics software, you need to look at what’s going on with your data right now. Here’s what to pay attention to:
What Data Are You Collecting Today?
List all kinds of data your factory already captures. Common examples include:
Production logs - start and end times of batches, throughput, operator input
Inventory levels - raw materials, work-in-progress, finished goods
Downtime tracking - reasons for downtime, outage durations
Scrap and quality data - reject reasons, inspection results
Order tracking - job status, completion time, quantities, delivery estimates
Once you go through the above, you’ll realize you have more data than you used to think you did.
Where Does This Data Live?
This is the point where gathering your data gets difficult. Data can be scattered across:
ERP systems that store your core business data
Manufacturing execution systems (MES) or supervisory control and data acquisition (SCADA) systems on the plant floor
Manual spreadsheets updated at the end of each shift
Standalone databases or legacy systems still in use
Cloud apps like inventory tools or supplier portals
The problem with these systems is that they’re often not connected to each other. So while the data exists, it’s not easily accessible.
Who Uses It, and How Often?
Next, think about your team. Knowing who uses what (and how frequently) helps you understand which systems are truly supporting decisions. And which ones, on the other hand, are just collecting dust.
Defining the Right KPIs and Metrics
Now that you’ve taken control over the data you have, you need to make it meaningful. To do this, define the right manufacturing KPIs. These shouldn’t be some generic metrics. Instead, they should clearly reflect what you measure and why.
How to Match Metrics to Roles Within the Business
Not everyone in your company needs to see the same numbers. A production supervisor and a chief financial officer are going to care about very different things. And that’s how it should be.
The most effective manufacturing data analytics dashboards are role-specific. They’re built around the problems each worker of your team needs to solve. That’s why you should consider who this dashboard is for and what they need from it.
Examples of Role-Specific Manufacturing KPIs
To make it easier for you to connect metrics to specific roles, here are the most common examples:
Operations
These employees work on the floor. Their dashboards should likely focus on the following:
Overall equipment effectiveness (OEE) - a metric that combines availability, performance, and quality to measure how effectively your machines operate
Machine downtime - this tracks when machines go down and why so you can target the right fixes
Units per shift - a way to measure how many units are being produced within a given work period
Quality Control
QC teams focus on making sure your products meet specifications and customer expectations. Their dashboards need to highlight:
Defect rates - broken down by machine, shift, product type, etc.
Batch traceability - the ability to trace raw materials and processes tied to specific batches
First-pass yield - measuring how many units meet quality standards the first time through without rework
Executives
Leadership typically needs to see the big picture: profitability, efficiency, and resource optimization. They need metrics like:
Overall efficiency - insight into how well the factory is performing
Cost per unit - measures how much money a company spends on producing each unit they sell
Inventory turnover - calculates how quickly inventory is sold and replaced over a given period
Laying the Groundwork: Integrations and Data Sources
Moving from spreadsheets to real-time dashboards may sound like a front-end project. But it’s way more than building a UI. What really powers manufacturing analytics is the back end: the data foundation.
So before you get any dashboards built, you have to connect your existing systems. The good news? You already have the data. But the downside is that it’s often siloed, underused, or plain hard to reach.
Manufacturers Already Use ERP, MES, WMS, and IoT Systems
Today’s manufacturers are supported by a mix of enterprise solutions:
ERPs manage financials, orders, and supply chains
MESs track production processes and performance
WMSs handle warehouse operations and inventory
IoT systems monitor equipment status, temperature, cycles, and more
The technology is there. The challenge is getting it all to work together.
The Issue Isn’t Data Collection — It’s Fragmentation and Poor Usability
The real obstacle isn’t a lack of data. It’s that everything lives in its own little world. Your MES might have minute-by-minute machine data, but good luck matching that with inventory levels from your WMS or job costs from your ERP.
Native Dashboards Are Narrow and Don’t Provide Cross-Functional Visibility
Sure, most systems come with their own dashboards. But they only show you a part of the data you might leverage.
Your ERP might display the order fulfillment status. Your MES might show downtime trends. But none of them give you a complete view of what’s happening with production, inventory, and quality.
The consequence? You have to piece together multiple screens (or, worse, reports) just to answer a basic question.
A Smart Analytics Solution Unifies All Data Streams into a Real-Time, Actionable View
Here’s what you actually need: a single dashboard that pulls live data from all your core systems - ERP, MES, WMS, sensors - and filters it based on who’s looking. Your quality manager sees first-pass yield by shift, your ops lead sees OEE by line, and your executives see cost per unit.
Manufacturing predictive analytics software offers no fluff. You cut time spent scrolling through reports. You reduce errors and fix issues before they become huge problems. And, of course, your team starts making faster, smarter decisions right from the shop floor.
Choosing the Right Tech Architecture
You know that connected data is key. But what’s also important is the architecture of your industrial analytics software. Speaking of that, you’ve got the following options:
Web-based vs. desktop vs. mobile dashboards. Consider how and where your team needs to access real-time production insights. Web-based dashboards are typically the most flexible — they’re accessible from anywhere and don’t require local installations. Desktop solutions are more powerful for heavy analysis but are tied to a specific machine. Mobile dashboards are handy for supervisors on the move. Ideally, your architecture should support all three.
Cloud vs. on-premise deployment. Cloud-based factory analytics tools are perfect for their scalability, lower upfront costs, remote access, and easier integration with other systems. On-premise solutions, on the other hand, give you more control over your data, which is especially relevant if you have strict compliance and data security requirements. Some manufacturing analytics companies go hybrid: core systems stay on-premise, but dashboards are cloud-based.
Real-time vs. scheduled updates. When we talk about “real-time” dashboards, we mean data that’s updated near-instantly as events happen on the shop floor. It’s critical for production and operations. That said, not every role needs live data. Scheduled updates might be fine for executive reports or financial summaries.
User access levels and permission management. Think about which role sees what. Not every user should have access to every dashboard or dataset. Operators should see their line’s performance - not full financials. Executives don’t need to explore every defect in the product (unless they want to).
Working with a Development Team
With your architecture planned, you can finally build your real-time dashboard. That usually means working with manufacturing data analytics companies or development teams.
The Benefits of Custom Development
Building a custom dashboard with a manufacturing software development company brings the following perks:
Custom workflows. Every factory is different, and so are its operations. A custom dashboard reflects your specific workflows, from shift changeovers to maintenance alerts.
Visual clarity. Off-the-shelf dashboards often pack too much - or not enough - information into the screen or don’t show the data you really need. A custom solution lets you create the visual layout you want.
Integration with your existing systems. A dev team can connect the systems you’re using and make them exchange data freely. This tight integration ensures your dashboards are real-time and reliable.
What to Expect When Working with a Dev Team
A dev team supports you throughout the entire dashboard development process - and even after it’s complete:
Discovery. Developers study your workflows, your goals, and the data you’re working with.
Prototyping. Experts create mockups or wireframes to make sure the design makes sense before any code is written.
Development. That’s where integrations get built and dashboards take shape.
Testing. Before deployment, testing ensures that your systems exchange data easily and users can actually use the tool.
Rollout. This usually starts with a pilot team before scaling across your whole operation.
Continuous improvement post-launch. Once your dashboard is in use, you’ll likely identify new needs or features to add. A dev team will stick around to help you iterate.
Conclusion
Data analytics in manufacturing shouldn’t go down to spreadsheets and disconnected systems anymore. It can get a powerful twist with real-time dashboards.
But as you’ve seen, smart manufacturing solutions aren’t just about creating a sleek UI. They’re about gathering a strong data foundation, connecting your systems, defining the right KPIs for each role, and building architecture that supports how your teams work.
You already have the pieces in place - ERPs, MES, sensors, and reports. All you have to do is stick them together with the right partner. For that purpose, contact Integrio Systems. Count on our 12-year expertise in custom manufacturing software development, including predictive maintenance and data analytics solutions.
Contact us
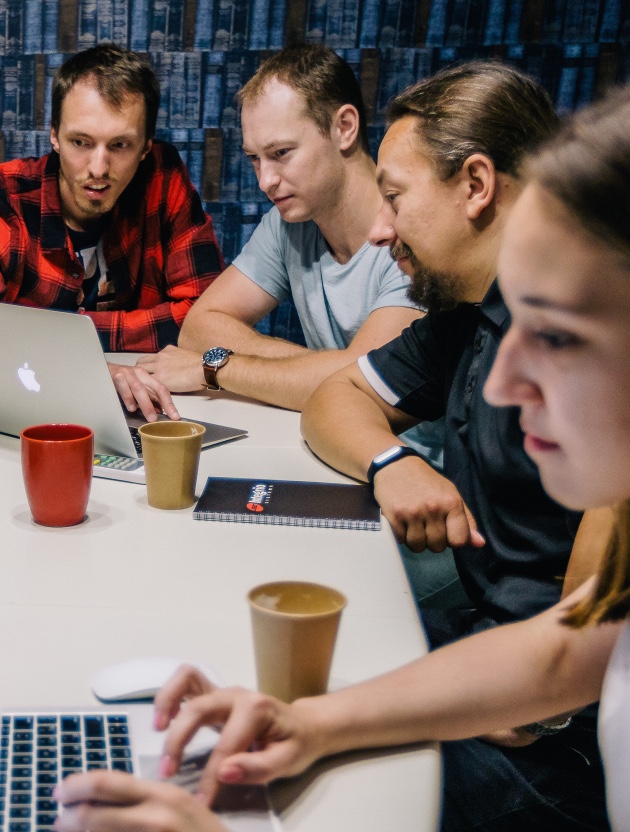