IT Strategy for Sustainable Growth: A 4-Year Plan for Mid-Sized Manufacturers
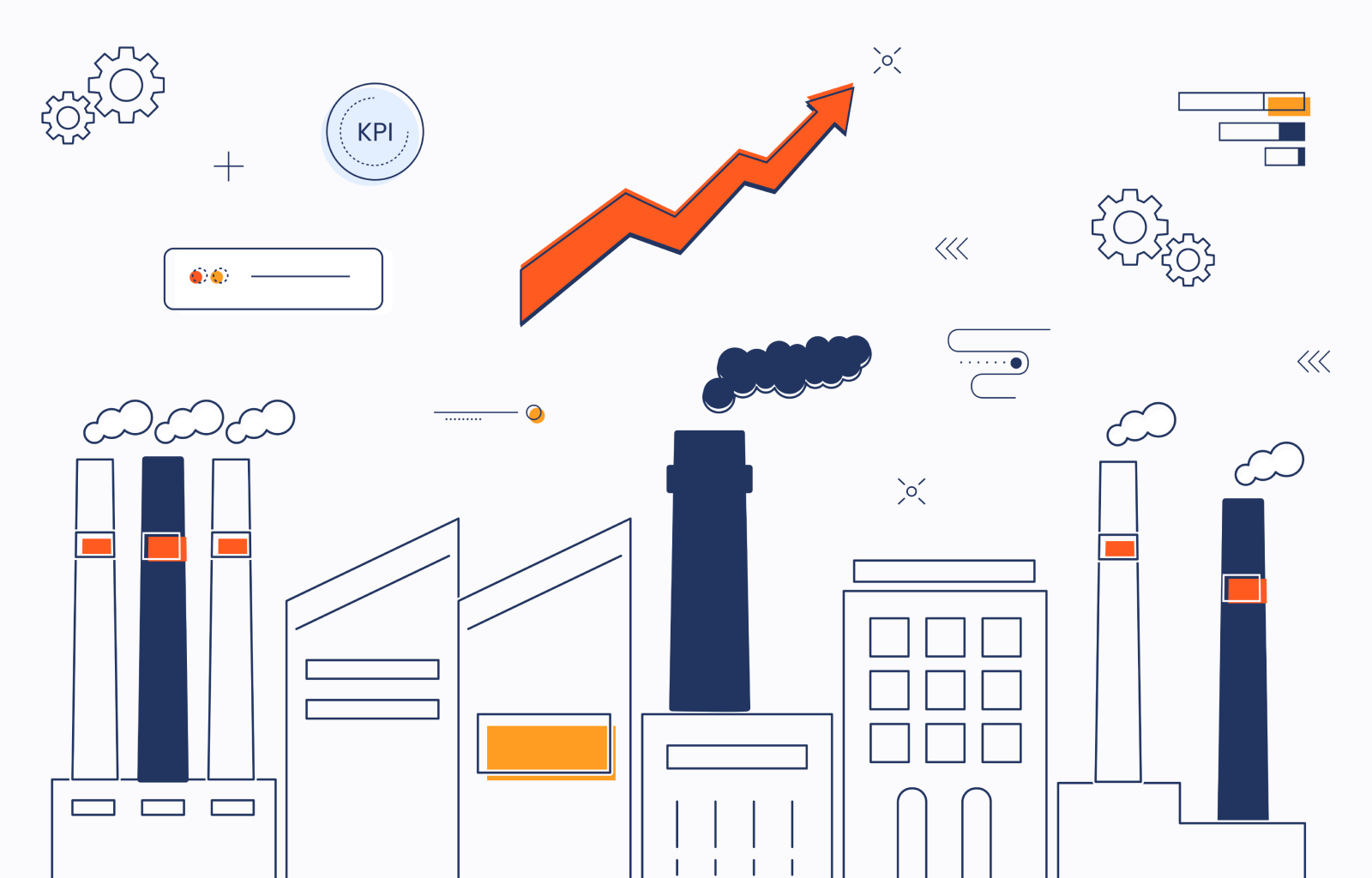
Manufacturing companies at the mid-market level face a few critical challenges. One is building robust IT systems that can scale as they grow while working within practical resource constraints. And it doesn’t matter whether you’re managing multiple production lines or expanding into new markets. Your IT infrastructure needs to evolve systematically.
After years of experience with custom software development for the manufacturing domain, our team has gathered numerous insights into handling IT growth challenges. In this article, we’ll share a practical four-year strategic growth plan. You can use it as a framework for modernizing operations without disrupting current production or overwhelming your team.
Assessment and Planning (Year 1)
The first year lays the groundwork for successful transformation. This phase focuses on understanding your current position and planning your path forward. It should consider both immediate needs and long-term objectives. During year one, account for the following:
Business & IT Alignment: Engage with stakeholders from every department to understand their needs, challenges, and vision for the future. Include production managers, quality control teams, supply chain managers, customer service representatives, etc., in these discussions.
Current IT Infrastructure Audit: Listing your hardware and software isn’t enough. It’s critical to understand how well your systems serve your needs. Identify where your technology supports or hinders operations and what needs to be replaced.
Gap Analysis & Risk Assessment: Manufacturing environments often struggle with manual data entry between disconnected systems, lack of real-time monitoring, outdated security protocols, limited supply chain visibility, etc. Define your specific bottlenecks. These will be areas for improvement.
Governance & Compliance Review: Your IT strategy must consider industry regulations and standards. Work with your quality and compliance teams to document and integrate all requirements into your planning process. Doing it early prevents costly adjustments later.
Budget & Resource Planning: Break down costs into must-have improvements, strategic investments, and innovation initiatives. Consider both direct costs like software licenses and indirect costs like staff training and temporary productivity dips during implementation. Create a flexible budget that allows for adjustments.
IT Talent Strategy: Assess your current team’s skills against future needs. Plan for training existing staff. Identify roles you’ll need to fill. Consider whether external partners might handle certain functions better, especially for the roles you don’t need full-time.
IT Modernization & Development (Year 2)
Year two focuses on implementing the software modernization ideas and plans developed in year one. This is where your strategy starts delivering tangible improvements to your operations. It requires careful project management and clear communication with all stakeholders. The core tasks and activities for the second year include the following:
System & Software Enhancements: Upgrade outdated applications, enhance software interoperability, improve data accuracy, and integrate solutions that improve core workflows. Prioritize changes that reduce operational bottlenecks. Aim to provide a better user experience for employees and customers alike.
Cloud Utilization Strategy: Manufacturing often requires a hybrid approach. Keep critical production systems on-premises. Move supporting functions to the cloud. When choosing one, consider data latency requirements, regulatory compliance needs, disaster recovery capabilities, integration requirements, and cost.
Network & Infrastructure Improvements: Production equipment needs reliable connectivity, while data collection systems require sufficient bandwidth for real-time monitoring. To balance this, focus on building redundant systems for critical operations and ensuring your infrastructure can support new digital initiatives.
Cybersecurity Enhancements: Implement advanced access controls, security monitoring, and incident response systems. Set up network segmentation to isolate critical systems. Plan for regular security awareness training for all staff.
Process Automation & Integration: Focus on eliminating information silos. Automate data flow between systems. Reduce manual entry points. Create a single source of truth for operational data. This might include implementing APIs between systems or developing automated reporting tools.
Data Management & Analytics: Establish a robust data management framework. Use the tools that can handle the volume and variety of manufacturing data. Develop customized dashboards for different user groups. Focus on building predictive maintenance capabilities using historical equipment data and performance patterns.
Innovation & Sustainable Growth (Year 3-4)
The final two years focus on applying and calibrating your modernized foundation for continuous improvement and innovation. This phase builds on your earlier investments to drive operational excellence and competitive advantage. The processes that take place here are:
Enhancing Digital Capabilities: Explore technologies that can give you a competitive edge. Focus on practical innovations that solve real problems rather than chasing trends. Each new technology should demonstrate clear value to your operations.
Customer Experience Improvement: Clients expect excellent service throughout the customer journey. Consider introducing customer portals for order tracking and management, automated quality reporting systems, real-time production status updates, and digital collaboration tools.
Operational Optimization: Use your advanced analytics to drive continuous improvement. Identify production bottlenecks. Optimize resource usage across operations. Improve quality control through predictive analytics. Reduce waste through better planning and enhance maintenance scheduling.
Sustainable IT Practices: These include optimizing energy usage in your data centers, implementing efficient printing policies, and ensuring proper disposal of electronic waste. Sustainable practices reduce costs and boost operational efficiency.
Security & Compliance Upkeep: Regular security assessments, updates to policies and procedures, and regulatory compliance maintenance ensure that your modernized systems stay protected. Make security awareness a part of your company culture, and check whether all employees understand their role in protecting company assets.
Ongoing Workforce Development: Keep your technical teams aligned with evolving industry demands and technological progress. Create comprehensive training programs covering technical skills and business processes. Develop clear career progression paths that encourage continuous learning and specialization.
Key Performance Indicators (KPIs)
Measuring the success of your IT strategy requires a comprehensive set of metrics. They need to evaluate both technical performance and business impact. Below, we’ll share several metrics you can track and explain how to calculate each.
IT & Business Alignment Score
This is a composite score measuring how well your IT initiatives support and drive business objectives. It typically combines several weighted components to create a single measurement on a scale of 0-100. You can consider factors such as project success rates, stakeholder satisfaction, investment alignment, and time to market.
For example, if a manufacturing line upgrade project aimed to increase production by 15% and achieved a 12% increase, it might score 80 points in the project success category. Similarly, if 85% of business stakeholders report satisfaction with IT services, this would contribute 85 points to the satisfaction component.
Efficiency Improvements
Efficiency Improvements track the tangible operational gains resulting from IT investments. This metric focuses on quantifiable changes in productivity, resource utilization, and cost savings. It is measured in specific units—time, money, and often percentage gains.
Calculation methods vary by specific metric. They typically compare baseline measurements against post-implementation results. For instance, here’s a formula for manufacturing cycle time reduction:
Improvement % = ((Original Cycle Time - New Cycle Time) / Original Cycle Time) × 100
Cybersecurity Readiness
This metric evaluates your readiness to prevent, detect, and respond to security threats. It can combine both preventive and reactive measures. The readiness score is typically calculated using a weighted framework. It considers various security controls and their effectiveness.
Suppose you have implemented 90% of the required security controls. You achieved an 85% employee training completion rate. You maintain a 95% patch compliance rate. All would be weighted according to their importance in your security strategy.
Process Optimization Metrics
They measure improvements in operational workflows and system integration, quantifying the impact of your digital transformation on daily operations. To calculate these, establish baseline measurements before optimization and track changes over time. For example, to measure data entry error reduction:
Error Reduction % = ((Previous Error Rate - Current Error Rate) / Previous Error Rate) × 100
Other process metrics include data accuracy, system integration, workflow efficiency, resource allocation, quality control, and documentation.
Customer Satisfaction Index
This index measures how technical improvements affect the customer experience. It combines various customer-facing metrics into a single score. The latter reflects overall satisfaction with your digital services and capabilities. Calculate this index using weighted averages of different satisfaction metrics on a scale of 0-100. For example:
Customer Satisfaction Index = (Delivery Performance × 0.3) + (Order Accuracy × 0.3) + (Response Time × 0.2) + (Service Quality × 0.2)
You can also include things like issue resolution, digital tool satisfaction, and other parameters in this formula.
Adoption of Practical Innovations
This metric evaluates how effectively your organization implements and benefits from new technologies. To calculate adoption rates, measure active usage against total potential users. For value delivery, you can compare actual benefits against projected returns. Here’s an example of a formula that falls under this category:
Innovation ROI = ((Benefit from Innovation - Cost of Innovation) / Cost of Innovation) × 100
Conclusion
A successful IT transformation in manufacturing requires more than just technology upgrades. It demands a thoughtful balance between modernization and operational stability. Our four-year strategy provides a structured approach to building robust, scalable systems that can improve your manufacturing processes and support your growth objectives.
As you implement this strategy, maintain flexibility to adapt to changing business needs while staying focused on your core objectives. The key lies in making deliberate, measured improvements that deliver clear value at each stage. And remember: success depends a lot on clear communication with all stakeholders and regular progress assessments.
Contact us
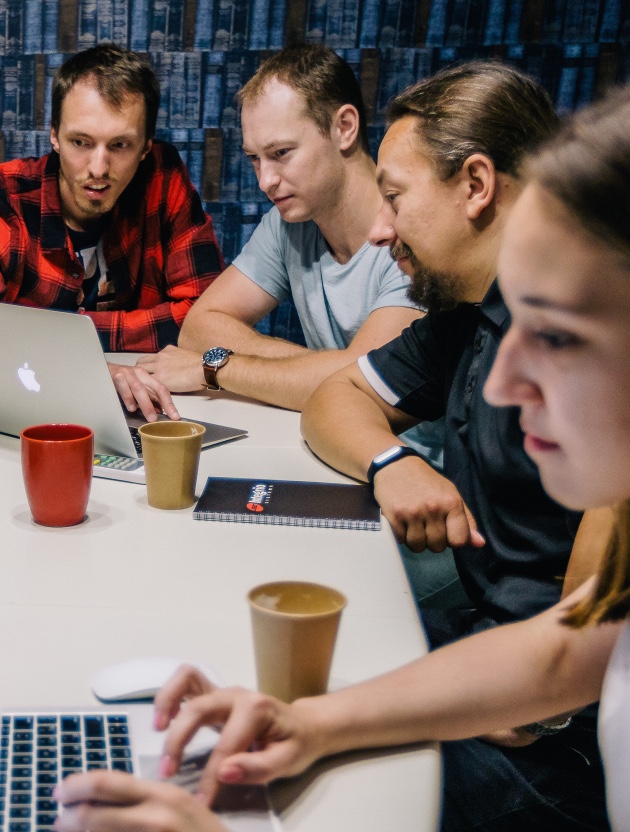