Custom AI Solutions for Predictive Maintenance in Heavy Industries
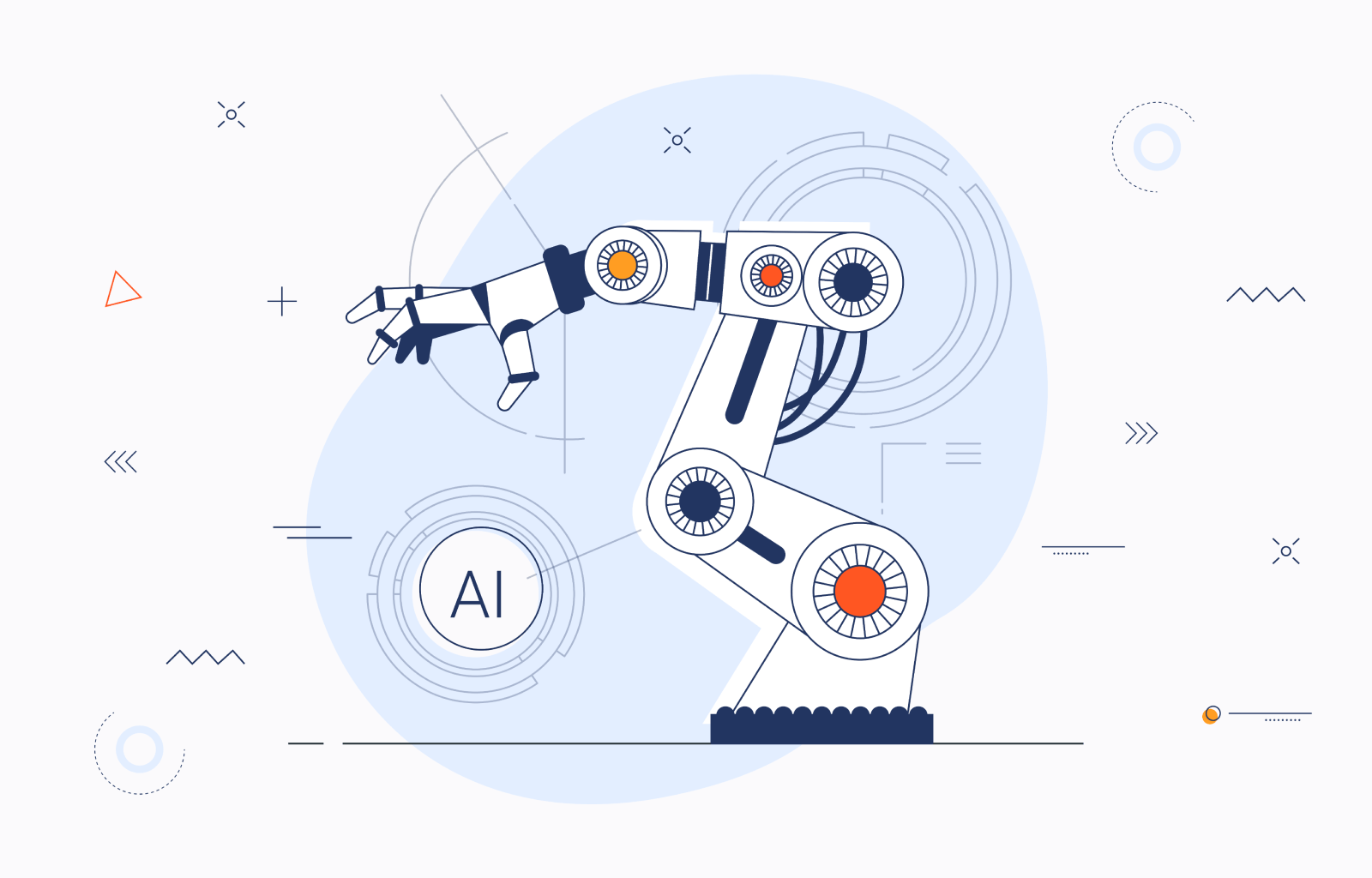
Predictive maintenance uses data and analytics to foresee potential equipment failures before they become critical. It involves sensors, data collection, and AI algorithms to help businesses optimize machinery performance, reduce repair costs, and minimize downtime.
Heavy industries relied on traditional maintenance practices for a long time. Specialists are used to taking action only after machinery. This approach failed because it usually resulted in high costs and unplanned downtime. Or they would arrange scheduled inspections and part replacements to reduce the chance of failure, which lacked flexibility.
Now, reactive and preventive methods are giving way to AI-powered predictive maintenance. In industries such as manufacturing, mining, oil and gas, and energy, specialists focus on the actual condition of the equipment. This transition enhances operational efficiency, safety, and stability.
How AI Enhances Predictive Maintenance
AI has ushered in the fourth wave of the industrial revolution, integrating digital technologies with physical systems to enhance efficiency and productivity. Here is how it is transforming heavy industries.
Data Collection & Monitoring
AI-driven predictive maintenance starts with continuous data collection from machinery through sensors. These sensors track various parameters, such as temperature, vibration, pressure, and energy consumption, and provide real-time insights into the condition of equipment.
In industries like oil and gas, monitoring the temperature of pipelines or vibration levels in pumps helps detect potential risks like leaks or mechanical wear. Such early detection allows businesses to schedule timely maintenance, thus preventing critical issues that could halt operations. In manufacturing, sensors on a production line detect subtle vibrations indicating potential mechanical wear.
By constantly monitoring this data, AI algorithms can detect anomalies early, allowing maintenance teams to intervene before minor issues escalate into large-scale failures. Taking a proactive approach reduces expensive downtime and ensures that the machinery works at its best.
Machine Learning Algorithms
Machine learning algorithms analyze historical and real-time data to identify trends, patterns, and anomalies. They learn from the new data collected to improve predictions over time, refining their accuracy.
In large-scale energy plants, AI models trained on historical data can anticipate equipment malfunctions based on subtle shifts in operational behavior, such as pressure drops or increased energy consumption. AI helps companies prioritize maintenance for high-risk components, reducing the chance of machinery failure.
In the energy sector, machine learning models predict the remaining useful life of wind turbine components based on past operational data, enabling timely replacement and minimizing disruptions. This capability allows businesses to schedule maintenance activities during planned downtimes, avoiding sudden breakdowns and ensuring continuous productivity.
IoT Integration
Integrating Internet of Things (IoT) devices with AI technologies creates a connected ecosystem where data flows seamlessly between equipment, predictive models, and maintenance teams. In mining industries, machinery operates in remote or hazardous environments, and IoT devices enable real-time monitoring from centralized control rooms.
This connection allows AI systems to instantly analyze data from multiple sources, providing a comprehensive view of machinery conditions. When an anomaly is detected, AI can trigger automated alerts, send notifications to technicians, or even initiate corrective actions, such as adjusting equipment settings, without human intervention.
Cost Savings
AI-driven predictive maintenance leads to substantial cost savings by reducing direct and indirect expenses. Direct savings arise from addressing issues before they lead to costly repairs or equipment replacements. Indirect savings come from avoiding production delays and reducing unplanned downtime, which could otherwise result in lost revenue.
Early detection of pipeline corrosion prevents costly leaks in the oil and gas industries. Scheduling maintenance based on equipment conditions helps use resources efficiently, making the business model more sustainable and cost-effective.
Benefits of Custom AI Solutions for Predictive Maintenance
As industries seek to enhance equipment maintenance, AI-driven predictive maintenance has emerged as a game-changer. While off-the-shelf AI tools offer general benefits, custom AI solutions provide significant advantages by addressing the specific needs of each industry.
Tailored to Industry-Specific Needs
High-precision manufacturing may require AI models that detect minute changes in machinery. At the same time, mining operations may need AI that handles data from harsh and hazardous environments. Similarly, large-scale energy plants may require AI to manage complex data from numerous systems running simultaneously.
Custom solutions account for these differences, allowing companies to focus on the specific operational challenges. This level of customization ensures that the AI system is accurate and highly relevant to the particular industry.
Improved Accuracy and Efficiency
Custom AI solutions target specific data patterns and operational behavior. By training AI with data from the actual equipment in use, businesses can more accurately detect subtle signs of wear, component fatigue, or other potential issues compared to generic AI models.
This level of precision is especially crucial in industries where equipment is highly specialized, such as mining or chemical manufacturing. Predictive maintenance tailored to the unique needs of these sectors ensures that even minor irregularities are detected and resolved quickly, helping maintain safety standards and compliance with industry regulations.
This results in fewer false alarms, higher prediction accuracy, and timely maintenance alerts. Improved accuracy leads to better decision-making, ensuring that maintenance actions are taken at the right time to prevent failures and extend the lifespan of machinery.
Integration with Existing Systems
A significant advantage of custom AI solutions is their ability to integrate seamlessly with existing enterprise systems like ERP (Enterprise Resource Planning), CMMS (Computerized Maintenance Management Systems), and IoT networks. This integration ensures a smooth transition to AI-powered predictive maintenance, with data flowing efficiently across different platforms.
When AI solutions connect directly with existing systems, businesses can continue familiar workflows and benefit from advanced predictive insights. This compatibility reduces disruptions and simplifies the adoption of predictive maintenance practices.
Better Return on Investment (ROI)
Compared to off-the-shelf software, custom AI solutions may involve a higher initial cost, yet they offer better long-term ROI by providing precision, reliability, and adaptability. They enable companies to avoid costly repairs, minimize downtime, and optimize maintenance schedules.
Generic AI tools often overlook specific operational nuances, resulting in less accurate predictions and potentially higher long-term expenses due to missed issues or unnecessary maintenance actions. With custom AI, companies invest in a solution that evolves with their operations, continuously improving performance.
Integrio’s Experience with Heavy Industries
The heavy industry often resists innovation, preferring traditional ways of operating. However, the sooner new technologies are adopted, the more beneficial they are for any business. For a compelling example, look no further than Cam Tran, a Canadian industry leader in manufacturing and refurbishing oil-filled distribution transformers.
The company successfully transitioned from conventional processes to modern solutions by implementing the custom ERP system Jive. This transition optimized the production cycle and significantly improved operational efficiency.
In 2014, when Cam Tran needed a custom software application for their business, they partnered with Integrio Systems to create Jive. It started as a specialized tool for organizing and controlling standardized work instructions but quickly evolved into a comprehensive ERP system.
Its evolution has delivered a competitive advantage for Cam Tran, allowing it to maintain better control over its manufacturing process, predict production volumes, and manage projects effectively. With instant access to KPIs, critical customer information, and real-time progress updates, Cam Tran teams can make informed decisions that drive performance and meet customer expectations.
Today, Jive goes far beyond primary work instruction management. The system supports quality control, internal audits, inventory management, winding schedule optimization, and financial forecasting.
Industry experts recognize Jive's intuitive and user-friendly interface. Auditors from BC Hydro praised Jive as a best-in-class platform for production control. This shows how a well-designed custom application can be a game-changer for businesses aiming to stay ahead in competitive industries.
If your company is ready to take the next step in operational excellence, including leveraging AI in predictive maintenance, Integrio is here to help. Our expert team specializes in creating custom solutions, particularly AI-based ones, that address your unique challenges and help you optimize your workflows.
Ready to get started? Contact us today to discuss how a custom application can become the next competitive advantage for your company! Build the future of your operations together with us.
The Role of AI in Advancing Industry 4.0
AI-driven predictive maintenance is a fundamental element of Industry 4.0, enabling the creation of "smart factories" that operate with greater efficiency and intelligence. This approach optimizes machinery performance, minimizes downtime, and extends equipment lifespan, laying the foundation for factories where data-driven insights enable autonomous decision-making.
AI and IoT: The Backbone of Industry 4.0
The technologies driving Industry 4.0, such as AI and the Internet of Things (IoT), work together to achieve this level of autonomy. IoT devices continuously collect data on equipment status, which AI systems analyze in real-time to detect patterns indicating potential problems. When issues arise, AI can automatically initiate maintenance actions or alert human operators, shifting maintenance from a reactive to a proactive and predictive process. This ensures continuous factory operations and reduces the chance of unexpected disruptions.
Examples of AI-Driven Predictive Maintenance
In the automotive industry, companies like BMW have adopted AI-driven predictive maintenance in their smart factories. By using sensors to monitor machine performance and AI algorithms to detect potential machinery wear, BMW can anticipate maintenance needs and schedule repairs during planned downtimes.
In the energy sector, GE applies AI-powered predictive maintenance to enhance wind turbine performance. Machine learning algorithms predict potential downtime and optimize energy output by analyzing data such as vibration and temperature. This approach is further supported by 'Humble AI', which allows the system to identify its own limitations and revert to safe operational modes when facing uncertainties, ensuring both reliability and efficiency.
In mining, Rio Tinto integrates AI with IoT devices to monitor equipment in remote locations. Real-time data from haul trucks and drilling equipment is analyzed using machine learning models to detect anomalies that could indicate mechanical wear. By leveraging predictive maintenance, Rio Tinto minimizes machinery breakdowns in challenging environments, ensuring operational efficiency and reducing costly disruptions.
Digital Twins and Robotics: Enhancing Smart Factory Operations
In smart factories, AI technologies integrate with other automation tools like robotics and digital twins. Digital twins create virtual replicas of equipment, allowing businesses to simulate maintenance scenarios and optimize repair schedules without affecting actual production. This synergy between AI, IoT, and automation tools improves operational efficiency and enhances the factory's ability to adapt quickly to changing conditions.
Empowering the Workforce and Future-Proofing the Industry
Embracing AI-driven predictive maintenance reduces the burden on human workers, allowing them to focus on more complex tasks that require strategic decision-making. This shift positions manufacturers for long-term growth and competitiveness, transforming the industrial landscape into a dynamic and resilient environment ready to thrive in the era of Industry 4.0.
Final thoughts
As heavy industries evolve, embracing AI-driven predictive maintenance is crucial for competitiveness. The shift from traditional maintenance methods to smart, data-driven approaches boosts efficiency, reduces costs, and lays the groundwork for Industry 4.0.
Custom AI solutions demonstrate the transformative power of tailored technology in optimizing processes and enhancing operational performance in heavy industry. Integrio has experience working in this sector, and also specializes in predictive analytics for healthcare and digital marketing, delivering customized solutions that help businesses leverage data-driven insights to improve decision-making and achieve better outcomes.
By addressing each maintenance issue proactively, companies can avoid disruptions and maintain smooth operations. These innovations have the potential to revolutionize how industries manage equipment and ensure a more resilient, flexible, and profitable future. Now is the time to take the next step toward operational excellence and secure your place in the industrial revolution. Reach out to us today to get help with your own journey.
Contact us
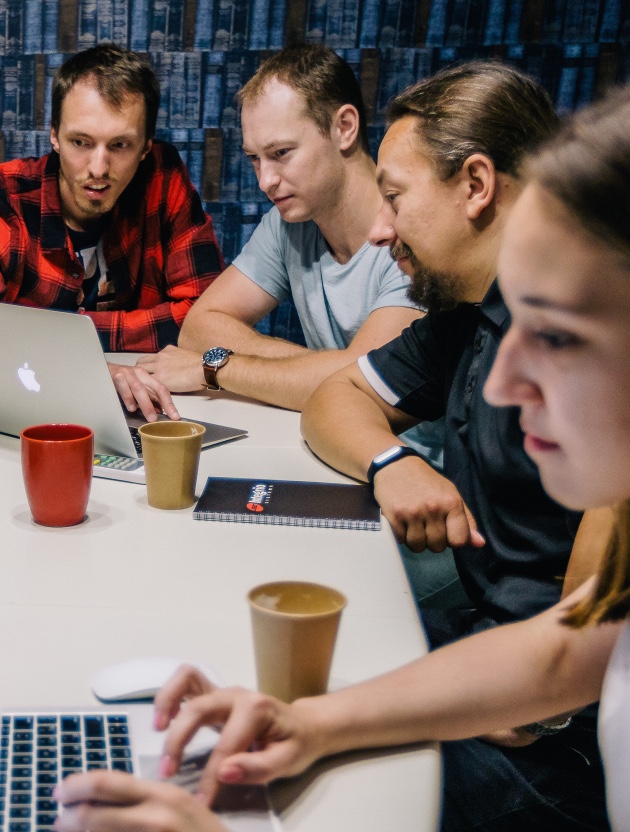