ERP Implementation Challenges and Best Practices for Canadian Manufacturers
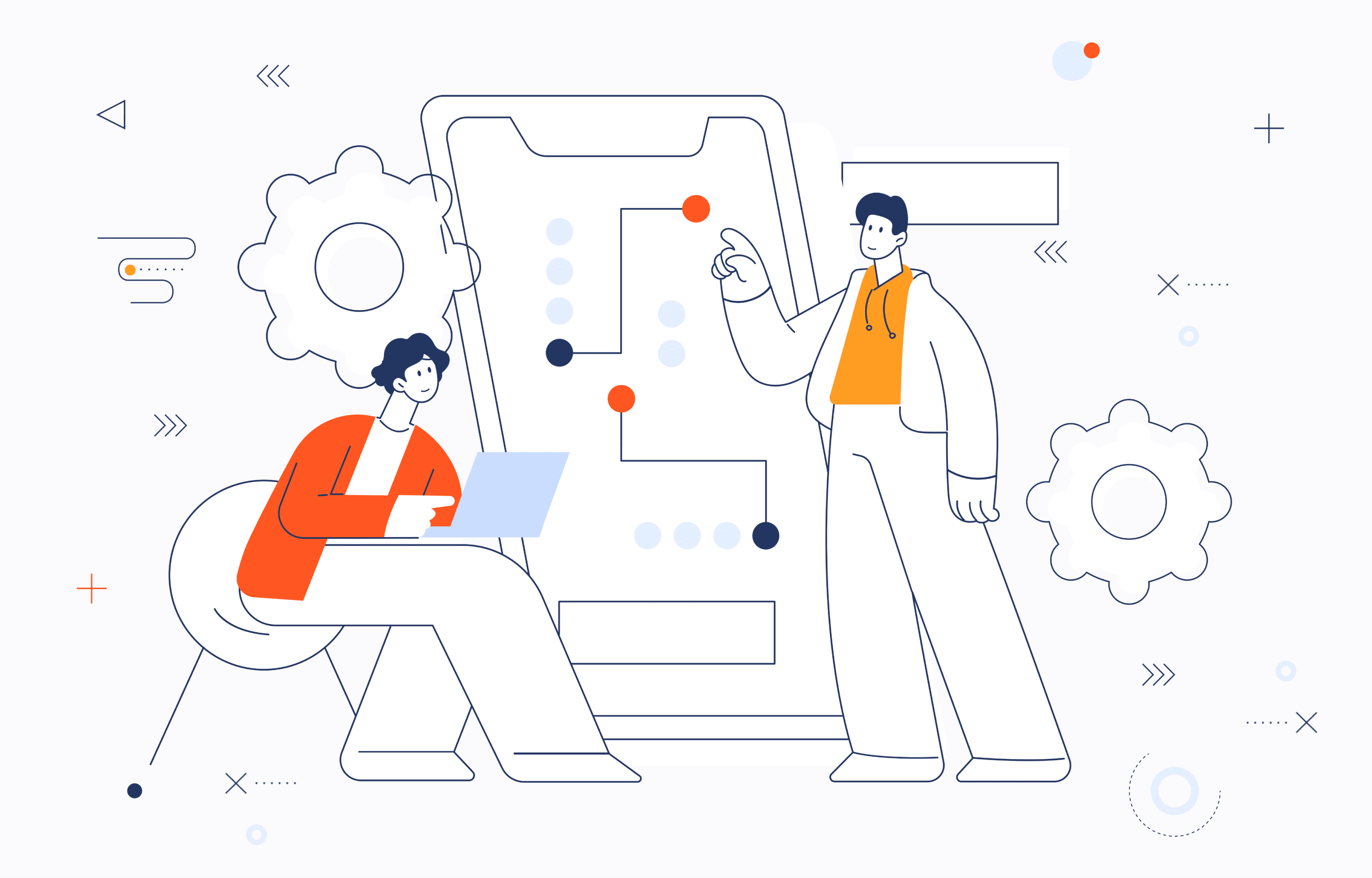
One in four businesses uses enterprise resource planning (ERP), and Canadian companies value strong security, cloud storage and processing flexibility, and industry-specific solutions. Manufacturing is leading the ERP adoption charge, accounting for one in three businesses using ERP globally. This is hardly surprising, as multi-faceted operations can benefit significantly from increased visibility, operational automation, and digitized quality assurance.
Yet, despite its benefits, ERP adoption isn’t always smooth. Many companies struggle with ERP implementation challenges. Usually, they arise from internal organizational factors, ranging from the poor choice of an ERP to communication breakdowns. Today, we’ll review the biggest ERP adoption issues and explain best practices for overcoming them.
ERP Definition and Benefits
ERP is a software solution that automates multiple business operations and streamlines decision-making. ERP systems usually combine accounting, human resources, purchasing, sales, inventory management, project management, and manufacturing modules. They contribute to a single database. Thanks to real-time data access and flexible reporting, ERP systems increase efficiency, reduce overhead, and improve the bottom line.
Depending on the ERP implementation goals, businesses can reap multiple benefits. For instance, ERP can accelerate payroll processing or help retailers stock the most fast-moving items for higher revenue. It’s especially helpful for manufacturers to keep track of parts and materials, uphold equipment maintenance schedules, and identify manufacturing bottlenecks to increase productivity. Integrating machine learning modules into ERP can also help with predictive maintenance, inventory management, shift scheduling, etc.
The ERP software market is worth around $200 billion. Its major players include Microsoft, Oracle, SAP, and IBM. However, there’s also a thriving market of customized ERP solutions for small and medium enterprises.
ERP Implementation Challenges for Canadian Manufacturers
Industry surveys claim that 80% of organizations achieved the projected ROI after ERP implementation. Some report improved customer or employee satisfaction; others note revenue increases. Still, an ERP implementation can be a hard one. So, let’s take a look at the biggest ERP implementation challenges for Canadian manufacturers.
Customization and Integration Failures
Most ready-made ERP solutions by Microsoft, Oracle, or SAP are complex systems with dozens of modules. Businesses must choose which modules to adopt and in what order, or they will face unmanageable expenses. Moreover, off-the-shelf ERP software typically caters to large businesses’ needs, making it unusable for small and medium enterprises.
Implementing the wrong modules and failing to adjust them to the organization’s reality can lead to significant operational disruptions. For example, failure to implement financial and payroll modules on time can lead to untimely wage payments and result in employee dissatisfaction. Differences in accounting practices can also prevent successful ERP implementation. These are just a few examples of how failed customization can disrupt business processes, leading to significant financial and reputational losses.
Change Management Shortcomings
Bombardier Aerospace discontinued the ERP implementation process in 2000 after sinking $130 million in software development, training, etc. Although the project suffered from many issues, weak business processes, insufficient employee training and lacking top management support were among the deciding factors preventing successful ERP adoption.
It’s a prime example of how critical change management is on all levels, from the C-suite to manufacturing employees. Resistance to new software implementation can result in safety breaches, unrealized efficiency potential, and direct financial losses.
Data Migration Breakdowns
Businesses can only enjoy the full ERP benefits when the system combines data streams from different departments and provides a single reference point across the organization. However, transferring data from legacy solutions can halt ERP implementation, as happened with Target Canada. The daily operations collapsed once the retail chain rolled out its SAP solution. Only about 30% of the legacy data was correct. Other items included false information about dimensions, weight, prices, vendors, etc. As a result, ERP implementation was delayed until the legacy information could be corrected.
Training and Support Issues
Human error is the core of most security breaches and failures in new software implementation projects. Without proper training, employees will not realize the ERP benefits, creating unpredictable bottlenecks that disrupt daily operations.
Friction can arise from employees’ comfortable familiarity with legacy software and their sabotaging ERP implementation. Another common issue arises from an insufficient consultant-to-employee ratio at the training stage. If workers fail to grasp the core functionality early, their efficiency will suffer long-term and mitigate the positive effects of ERP adoption.
Compliance and Regulatory Requirements
ERP systems are a prime cyber attack target because they host sensitive data, from payroll information to customer details. Unfortunately, ERP implementation mishaps can result in unforeseen security breaches. For instance, details about over 47,000 US-based Pacific Gas and Electric devices ended up online. The third-party vendor mistakenly used the information in a demo database without any security measures required in a real-life ERP application.
It could have caused big trouble for a Canadian manufacturer. Under PIPEDA (Personal Information Protection and Electronic Documents Act), Canadian businesses must report personal data breaches that may harm their employees or customers. Failure to report may result in fines of up to 100,000 CAD, reputation losses, and legal action.
ERP Implementation Guide for Canadian Manufacturers
Understanding the potential challenges of ERP implementation is vital for avoiding them. But that is only half the job. Let’s now consider the best practices to make ERP implementation run smoothly and achieve the expected ROI.
Create a Comprehensive Plan
Start with a clear and measurable goal for ERP implementation. It shouldn’t be vague or overly ambitious. Instead, make it as precise and achievable as possible. For example, reduce picking and packing speed by 15% or complete payroll twice as fast.
Once you have the primary goal, ensure all stakeholders are on the same page. You can hire third-party IT consultants to run the discovery stage of the project and take over requirements elicitation. Avoid introducing unnecessary changes after you approve the project's scope and budget. They will delay development and implementation and cause project and budget creep. Instead, acknowledge potential issues and account for them in your timeframe and budget planning.
Develop or Customize an ERP System
As we’ve established, the ERP landscape is pretty diverse, even if giants like Oracle and SAP dominate it. With your goal in mind, decide whether to use a ready-made solution or a custom-built ERP. Research potential vendors and their offers and discuss customization options.
Off-the-shelf solutions typically require significant upfront investment, and adjusting them to fit your needs requires extra spending. At the same time, implementation can be much faster than creating a new ERP from the ground up. Either way, you’ll need a reliable IT vendor with experience in manufacturing automation and an understanding of the industry.
Create a Data Management Strategy
ERP systems are designed to help transform businesses through data-driven solutions. So, data management is key for successful ERP adoption. You can start with these three steps:
Locate all the enterprise data. It can be dispersed across multiple spreadsheets, databases, applications, and even on paper. This is a critical step, as missing data can halt the ERP implementation and overall business operations.
Analyze and delete outdated information. ERP implementation can be a chance to eliminate obsolete data and improve operational efficiency by striking it from daily processes.
Structure and clean up data points. As all critical information will be stored in the ERP databases, it should use the same format and be free of duplicates and inconsistencies. Data validation is time-consuming but critical for continued operations upon ERP rollout.
If you complete these steps, migrating data to the new system should go smoothly. Still, running a test on a small data batch is a good idea to ensure ERP operations before migrating the rest of the databases.
Implement Effective Training Programs
Training is a critical part of the ERP rollout process. First, the employees should understand how they can benefit from new software. For example, if the warehouse management module helps them pick and pack orders faster, the workers should understand how the boost to company revenue will affect their wages.
Next, employees should have relevant training materials and have enough time to practice their new skills. Instead of making each worker go through the whole handbook, provide them with actionable step-by-step instructions, complete with video walk-throughs and FAQs. To avoid operational holdups, run the training before the ERP rollout to ensure everyone is ready to switch to the new system once it’s up and running.
Monitor and Improve the ERP Solution
Manufacturing isn’t static. Businesses must address new challenges to remain successful and sustainable, and ERP solutions should adapt and change accordingly.
After the initial implementation, analyze the project and decide if the primary goal is met. Look for and log the new system's advantages and drawbacks. Address all the bottlenecks and shortcomings in the next iteration. It should become an ongoing process with regular audits and reviews to ensure the ERP solution remains a good investment.
Case Studies and Examples
Following ERP implementation best practices and avoiding potential issues helps Canadian manufacturers reap the benefits of operational automation, as the following cases prove.
Cam Tran
Cam Tran is a prime example of a successful custom ERP development. The Canadian oil-filled transformer manufacturer implemented Integrio's Jive ERP system. The solution included a production and inventory management toolkit, financial and production forecasting tools, a custom KPI dashboard, and data management and storage solutions. Moreover, Cam Tran and Integrio continue working together to improve and adapt Jive ERP to new challenges.
Oliberté
Oliberté, operating the first fair trade shoe factory in the world, adopted BlueLink ERP to support its ongoing growth. The company lacked EDI (electronic data interchange) integration, critical for working with large retailers, and struggled with inventory management and pricing. Adopting the ERP helped the business automate many daily processes and grow by 100% year on year without any setbacks in manufacturing and order processing.
Ganong Bros. Limited
As the oldest candy company in Canada, Ganong Bros. Limited used Sage X3 ERP to bring its manufacturing and sales processes into the 21st century. The software helped improve inventory planning and implement software-based quality assurance processes. Moreover, the company gained insight into profit calculations and streamlined customer communication through EDI. Over two-thirds of Ganong Bros. domestic orders now come through EDI.
Conclusion
To reap ERP benefits, start by creating a comprehensive development and data migration plan and work on training employees. However, remember to keep an eye on the ERP system and upgrade it to address new challenges. These best practices will help you avoid ERP implementation issues stemming from poor understanding of its goals, wrong data migration decisions, and the lack of employee training. Careful planning can potentially save you years of lost time and millions of dollars.
Integrio has been helping Canadian manufacturers like Cam Tran adopt ERP solutions for years. Our expert team can help your business overcome any implementation obstacles, so contact us to schedule a consultation.
Contact us
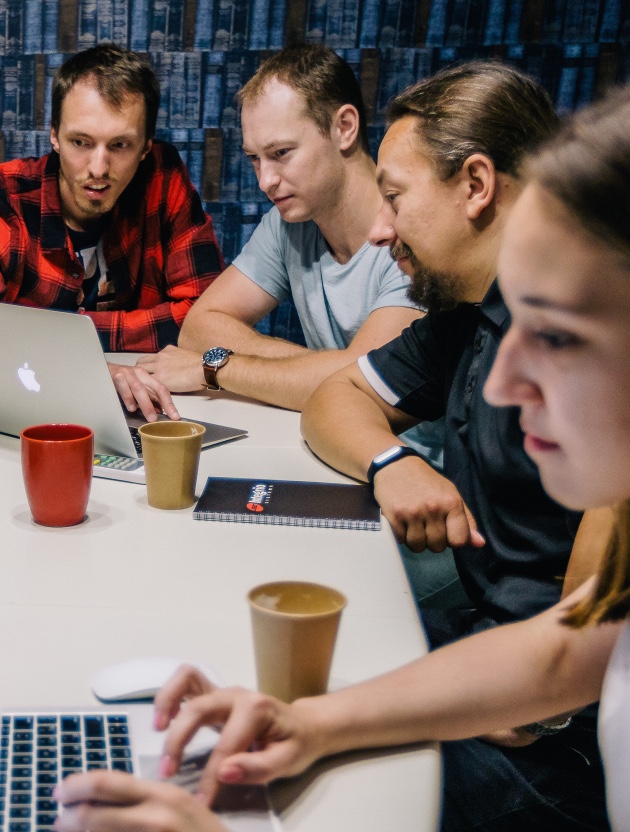